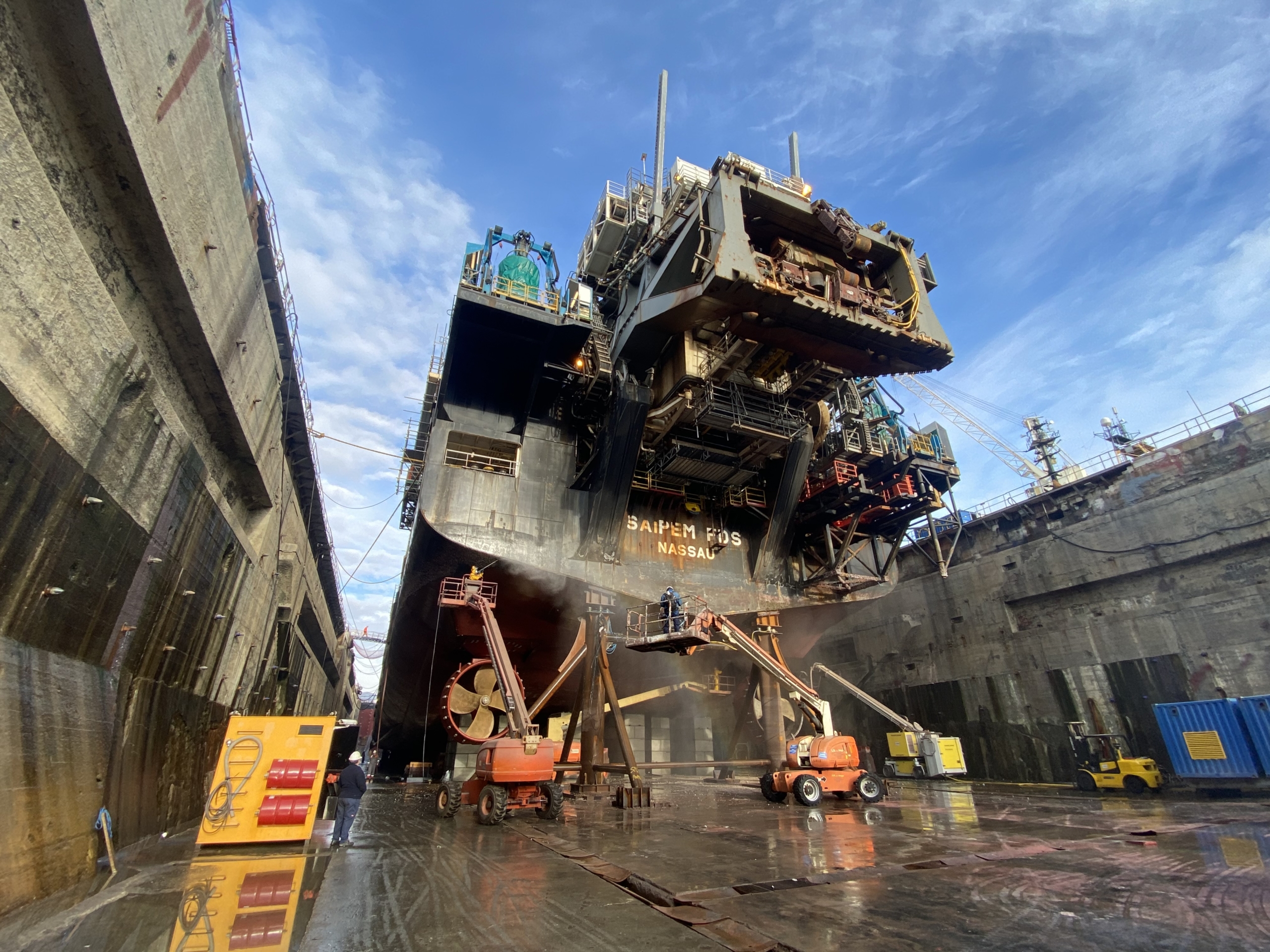
How an Impressed Current Cathodic Protection (ICCP) System Works
Modern hull coatings offer a degree of corrosion protection but cannot provide a complete solution. That’s why many operators choose a purpose-designed Impressed Current Cathodic Protection (ICCP) system to safeguard their vessels.
System Components and Operation
An ICCP system employs an array of hull-mounted anodes and reference cells that are connected to one or more control panels. These components work together to generate a controlled external current that effectively suppresses the natural electro-chemical activity on the hull’s wetted surface.
Key Benefits
- Prevents Aggressive Corrosion:
By neutralizing the formation of corrosion cells on the metal surfaces, the system reduces the risk of aggressive deterioration. - Compatibility with Dissimilar Metals:
ICCP systems mitigate the corrosion issues that can arise when dissimilar metals are joined by welding or are in close proximity (as seen with propellers and other components). - Enhanced Longevity of Hull Structures:
This proactive approach significantly extends the service life of the vessel’s hull and other critical components.
With an ICCP system, vessel operators enjoy a robust, long-term corrosion protection solution that complements modern hull coatings and enhances overall vessel integrity.
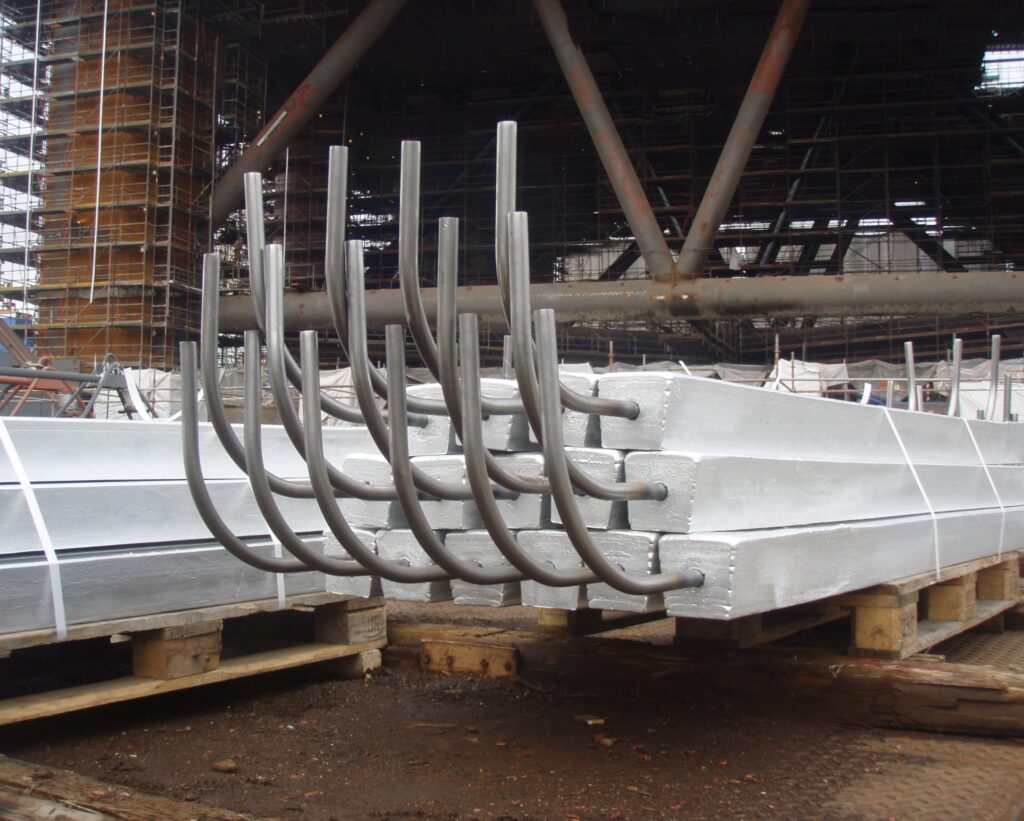
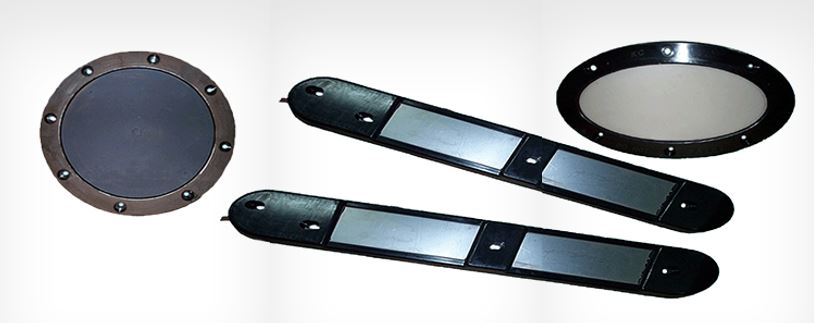
Enhanced Protection and Efficiency with ICCP Systems
ICCP systems are engineered to automate the current output while dynamically adjusting the voltage output. This adaptive approach ensures that the desired protection level is maintained even as seawater resistivity changes. Unlike sacrificial anode systems, where increased seawater resistivity can reduce anode output and protection, ICCP systems consistently deliver optimal performance within the standard range of seawater conditions.
Key Features and Benefits
- Adaptive Voltage Control:
The system continuously monitors the electrical potential at the seawater/hull interface, automatically adjusting the output to the anodes to maintain the correct protection level. - Superior Reliability:
By actively controlling the electrical potential, ICCP systems provide a consistent and reliable level of protection, far exceeding the capabilities of sacrificial anode systems, where protection levels are often unknown and uncontrollable. - Cost Savings:
Installing an ICCP system can significantly reduce hull maintenance costs and fuel consumption by maintaining a smooth hull surface, thereby improving vessel efficiency. - Enhanced Safety and Asset Protection:
With improved hull integrity and reduced corrosion, vessel operators can safeguard their investment and enhance overall safety.
Adopting an ICCP system not only delivers robust corrosion protection but also contributes to long-term operational savings and improved vessel performance.
See all ICCP products
Health Checks and ICCP System Performance
Maintaining the operational integrity of your ICCP system is critical to safeguarding your vessel’s hull and avoiding costly repairs. Improper commissioning, calibration errors, or system malfunctions can lead to significant dry dock expenses. By prioritizing annual maintenance and health checks, you ensure that your ICCP system operates at peak performance, ultimately protecting the longevity and safety of your vessel.
Key Benefits:
- Prevent Costly Downtime:
Regular inspections help identify and correct issues before they escalate. - Enhanced Safety:
A well-calibrated ICCP system strengthens hull integrity, contributing to overall vessel safety. - Long-Term Savings:
Consistent maintenance reduces the risk of severe corrosion, lowering long-term maintenance and repair costs. - Optimized Performance:
Routine health checks ensure the system continually adapts to changing seawater conditions, maintaining optimal protection.
Invest in the health of your vessel by scheduling annual ICCP system evaluations and maintenance. Ensure your ship remains protected, efficient, and safe for the long haul.
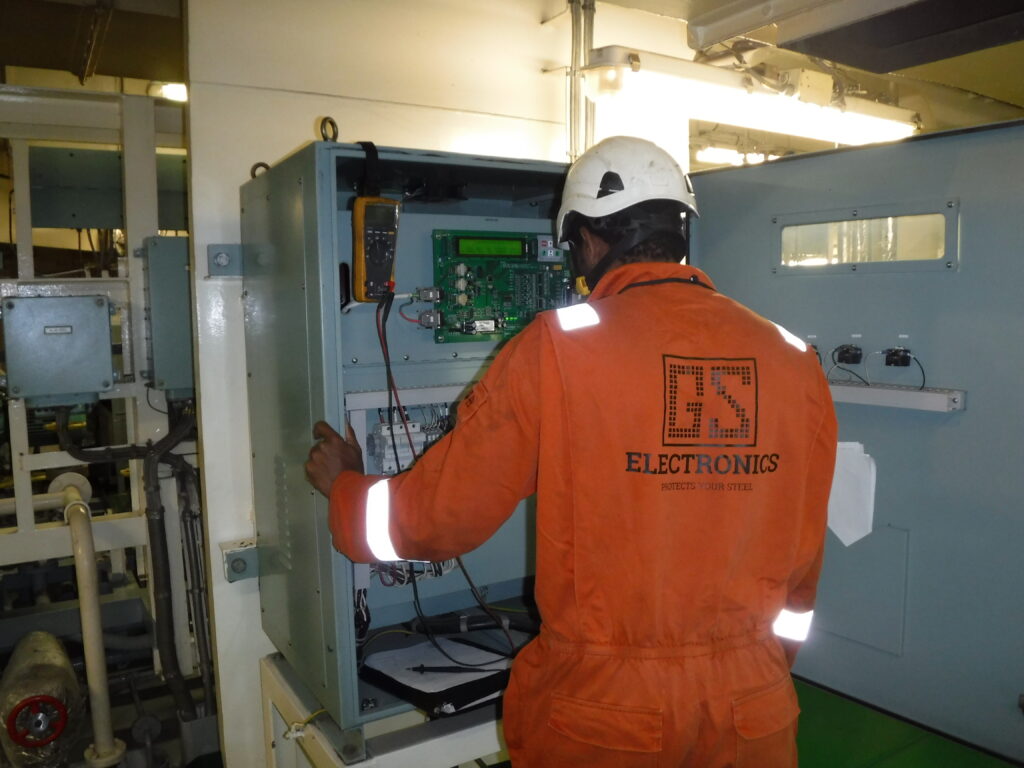
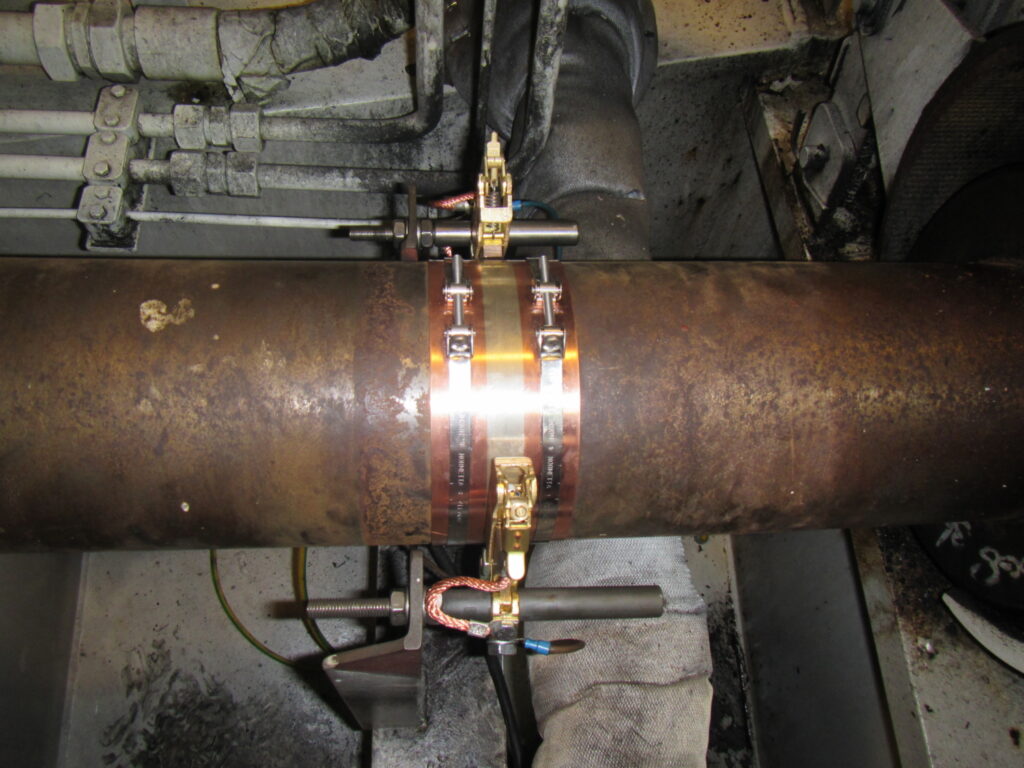
Shaft Earthing Device (SED) – Enhancing Propulsion and Engine Durability
Our high-efficiency Shaft Earthing Device (SED) is designed to prevent micro pitting on the propeller, as well as on the sliding surfaces of crankshaft journals and main engine bearings. This innovative system creates a controlled short circuit between the rotating propeller shaft and the ship’s hull, effectively mitigating spark erosion and ensuring long-lasting component integrity.
Key Features
- Optimized Electrical Potential Decomposition:
The SED features a split slipring, copper-lined with a silver track, ensuring excellent potential decomposition and consistent performance. - Reliable Contact Brushes:
Engineered with durable contact brushes that provide both lubrication and extended service life. - Ease of Installation:
Standardized parts and a high prefabrication grade allow for straightforward onboard installation by technical crew without the need for specialized tools.
Recommended Enhancements for Effective Operation
- Remote Indicator: Install a remote indicator for continuous monitoring, ensuring the overall system remains effective and any potential issues are promptly addressed.
- Automatic Slipring Cleaning Device:
Equip the system with an automatic cleaning device to maintain optimal performance by preventing increases in residual potential during operation.
The Shaft Earthing Device (SED) not only safeguards your vessel’s propulsion system but also contributes to overall operational efficiency and safety. Contact us today to learn more about how our SED solutions can enhance your vessel’s performance.
See all SED products